Carrier Solara Manual Transicold
Carrier’s Solara heater is a heating system specially designed to protect cargo transported in extreme low-ambient climates by heating cargo above a specified minimum temperature. Carrier’s micropocessor system in the Solara features virtually automatic operation-in a system that’s incredibly easy to use. Strategic up-front placement of serviceable components and a convenient swing-open, lift-off front door provides immediate access for faster, easier servicing and low cost maintenance. A modified bearing housing means extended engine life, particularly in rugged operating environments like inter-modal applications.
We are a proud dealer of Carrier Transicold equipment, the world's largest provider of heating, air-conditioning and refrigeration solutions. Contact us for your.

Other Features and Benefits:. Solara delivers a full 50,000 Btuh of heat and 3,200 CFM of airflow for premium cargo protection in today’s longer, wider thinwall trailers. Known for high performance, long life, and low maintenance, the Carrier CT2-29 engine also delivers more power output, maximum fuel economy and cleaner emissions.
. BOX TEMPERATURE FUNCTION START/RUN ENTER CHANGE AUTO S/S MANUAL UNIT PRETRIP STANDBY DATA CHECK DEFROST CONTINUOUS ENGINE OPERATOR’S MANUAL Ultra/Ultra XL, Ultima and Solara Beginning With S/N HAR90573670 And Extra/Ultra XT Trailer Refrigeration Units With Standard Microprocessors 62-10601 Rev G. OPERATOR’S MANUAL TRAILER REFRIGERATION UNITS WITH STANDARD MICROPROCESSOR.
CONTENTS Page Safety.Unit Identification. AFETY Your Carrier Transicold refrigeration unit has been designed with the safety of the operator in mind. During all pre-trip inspections, daily inspections, and problem troubleshooting, you may be exposed to moving parts; please stay clear of all moving parts when the unit is in operation and when the Start/Run-Off Switch is in the START/RUN position. If a problem occurs, please refer to the information on this decal, and make a note of the model and serial number before calling for assistance. This information will be needed when you contact a technician or Carrier Transicold Service Engineer so that they may properly assist you. Unit Identification Decal 62-10601.
PERATION TARTING NIT - FAULT FAULT STAND-BY START/STOP 8 8 8 8 8 8 8 8 8 8 8 8 8 8 8 8 8 8 8 8 8 8 8 8 8 8 8 8 8 8 8 8 8 8 8 8. STANDBY POWER ON SETPOINT. The microprocessor controller will run a self test. All of the mode lights will light, all of the segments on the display will be turned on. The display will then show the setpoint temperature on the left and the box temperature of the trailer on the right. The last character (after the degree symbol) shows the temperature units as F (Fahrenheit) or C (Celsius). TARTING NIT - ANUAL (C ONTINUOUS 1.
Place START/RUN - OFF switch to the START/RUN position. If START/STOP is displayed, press AUTO S/S-CONTINUOUS toggle key to place unit in Continuous Run Mode. Press FUNCTION CHANGE key until AUTO OP or MAN OP is displayed. Glow Time Engine Coolant Temperature Glow Time in Seconds TV/Short Engine Coolant Temperature (Default) Long Less than 32F (0C) 33F to 50F (1C to 10C) 51F to 77F (11C to 25C) Greater than 78F (26C) NOTE: When the unit is in Continuous Run mode and set for Manual Operation, the unit must be started manually WARNING Under no circumstances should ether or any other. RETRIP HECK FAULT FAULT STAND-BY COOL P P P P P P P P P P P P P P P P STANDBY POWER ON SETPOINT BOX TEMPERATURE START/RUN FUNCTION ENTER CHANGE AUTO S/S STANDBY UNIT MANUAL PRETRIP DATA CONTINUOUS CHECK DEFROST ENGINE.
Carrier Transicold Parts Manual
The PRETRIP mode is for checking unit operation and evaluating operation of all modes. The unit will cycle thru all modes of operation at 30 second intervals. When Pretrip is complete, Pretrip mode is terminated and the unit returns to normal operation. The final PRETRIP mode is Defrost. HANGING ETPOINT Press UP arrow key to increase displayed setpoint. Press DOWN arrow key to decrease displayed setpoint. FAULT FAULT STAND-BY -2 2 2 2 0 0 0 0.0 0 0 0 3 3 3 3 4 4 4 4.5 5 5 5 ° ° ° ° F F F F STANDBY POWER ON SETPOINT.
Setpoints of -22°F to +89°F (-30°C to +32°C) may be entered via the keypad. The controller always retains the last entered setpoint in memory.
If no setpoint is in memory (i.e. On initial startup), the controller will lock out the run relay and flash “SP” on the left hand display until a valid setpoint is entered. TART- PERATION START/STOP FAULT FAULT STAND-BY START/STOP -2 2 2 2 0 0 0 0.0 0 0 0 3 3 3 3 4 4 4 4.5 5 5 5 ° ° ° ° F F F F STANDBY POWER ON SETPOINT.
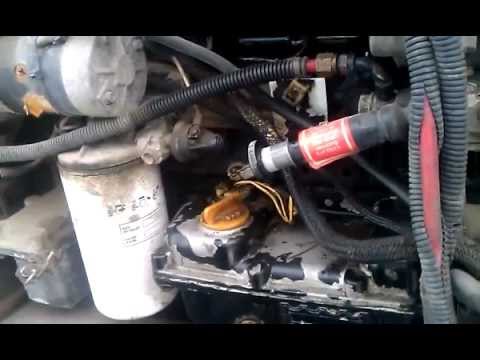
The unit will remain in low speed after engine start-up - 5 minutes for XT products, 10 minutes for all others. If the unit fails to start, shuts down on a safety, or fails to run for the minimum run time, three consecutive times, the fault light is on. ONTINUOUS PERATION START/STOP Must Not Be Displayed FAULT FAULT STAND-BY -2 2 2 2 0 0 0 0.0 0 0 0 3 3 3 3 4 4 4 4.5 5 5 5 ° ° ° ° F F F F STANDBY POWER ON SETPOINT. In the Continuous Run mode, the diesel engine will run continuously providing constant air flow and temperature control to the product. Continuous Run operation is normally used for perishable loads. Refer to R ECOMMENDED RANSPORT EMPERATURES (See Page 32). Start-Stop and Continuous operation may be tied to the setpoint ranges frozen perishable.
ANUAL EFROST DEFROST Indicator FAULT FAULT STAND-BY DEFROST -2 2 2 2 0 0 0 0.0 0 0 0 3 3 3 3 4 4 4 4.5 5 5 5 ° ° ° ° F F F F STANDBY POWER ON SETPOINT. The defrost mode may be initiated in three different ways if the evaporator coil is below 40°F (4.4°C): 1.
Defrost is initiated automatically at preset intervals by the defrost timer in the microprocessor. Defrost is initiated by the defrost air switch. UNCTION HANGE ARAMETERS 1. Press FUNCTION CHANGE key until Function to be changed is displayed. Press ENTER key.
FAULT FAULT STAND-BY D D D D E E E E F F F F R R R R 1 1 1 1 2 2 2 2.0 0 0 0 H H H H DEFROST STANDBY POWER ON. UNCTION HANGE ARAMETERS The following table has columns for Code and English displays. English is the default setting. Change Functional Parameter to Code to see Code display format. Function Codes CODE ENGLISH DATA DEFR Defrost Time Interval FN1 ON HIGH AIR High Air Flow FN1 OFF NORM AIR Normal Air Flow OFF T. FAULT FAULT STAND-BY s s s s u u u u c c c c t t t t COOL 2 2 2 2 5 5 5 5 P P P P STANDBY POWER ON SETPOINT BOX TEMPERATURE START/RUN FUNCTION ENTER CHANGE AUTO S/S. The following table has columns for Code and English displays.
English is the default setting. Change Functional Parameter to Code to see Code display format. Unit Data Codes CODE ENGLISH DATA SUCT Suction Pressure Engine Hours CoolantTemperature Return Air Temperature.CD5 Supply Air Temperature.CD6. LARM ISPLAY & ESET LARM ISPLAY When an alarm is on, normal display of Setpoint/Box Temperature alternates with alarm display. When fault light is on, check display for alarm message.

Press FUNCTION CHANGE key. FAULT LIGHT FAULT FAULT STAND-BY E E E E N N N N G G G G O O O O I I I I L L L L.
The following table has columns for Code and English displays. English is the default setting. Change Functional Parameter to Code to see Code display format. Display CODE ENGLISH ALARM DESCRIPTION ENG OIL Low Oil Pressure High Coolant ENG HOT Temperature HI PRESS High Pressure STARTFAIL. TANDBY PERATION For units equipped with electric standby: 1.
Place START/RUN-OFF switch in OFF position FAULT FAULT STAND-BY -2 2 2 2 0 0 0 0.0 0 0 0 3 3 3 3 4 4 4 4.5 5 5 5 ° ° ° ° F F F F COOL STANDBY POWER ON. Standby Operation is for Ultra NDM units only. Check for proper motor rotation. Condenser air must be drawn into unit. To reverse rotation, stop unit, disconnect power cord and change polarity of plug. TOPPING FAULT FAULT STAND-BY -2 2 2 2 0 0 0 0.0 0 0 0 3 3 3 3 4 4 4 4.5 5 5 5 ° ° ° ° F F F F COOL STANDBY POWER ON. The diesel engine will stop and the microprocessor controller will turn off.
NSPECTION The pre-trip inspection should be performed before picking up any load. This inspection is essential to anticipate and help minimize the possibility of “over-the-road” problems. These checks take only a few minutes. Place the unit’s main switch in the STOP (0) position. Over-all Unit - visually inspect the entire unit for leaks, loose bolts, frayed, loose, broken wires, etc. Radiator/condenser coils of the unit should be free of dirt, bugs, cardboard, or any other debris that may obstruct airflow across the coils.
Carrier Transicold Solara Manual
The evaporator (located inside the trailer) should be free of debris also, especially stretch-wrap, which is often used during transport to prevent cargo shifting. RODUCT OADING BEFORE LOADING: D Pre-cool the trailer. This will remove much of the heat from the inside of the trailer, and give the product better protection when it is loaded. D If possible, place the unit in a defrost cycle immediately before loading. Product stacking is another important factor in protecting the product.
Products that generate heat - fruits and vegetables, for example - should be stacked so the air can flow through the product to remove the heat; this is called “air stacking” the product. Products that do not create heat - meats and frozen products - should be stacked tightly in the center of the trailer. These are included for reference only and should not be considered preemptive of the setpoint required by the shipper or receiver. More detailed information can be obtained from your Carrier Transicold dealer.
Setpoint Range. If, however you run into problems the following section may be of assistance. If you do not find the trouble that you have experienced listed, please call your Carrier Transicold dealer for assistance. General Problems Unit won’t crank. USES The fuses that protect the circuits of the Microprocessor control system are located in the control box on the roadside of the unit. They may be accessed by loosening the screws that hold the control box cover closed. The cover can be removed and hung below the control box by its tethers as shown below.
AINTENANCE Engine oil - the oils recommended for use in your refrigeration unit must comply with the American Petroleum Institute’s (API) CI or higher rating or Mobil Delvac 1 synthetic oil. The use of any oil that does not meet this rating may affect the warranty on the engine in the unit. AINTENANCE CHEDULE For the most reliable operation and for maximum life, your unit requires regular maintenance. This includes oil and filter changes, fuel and air filter replacement, coolant replacement. Maintenance should be performed on the following schedule: ERVICE D Drain the engine oil and replace oil filter. Every 1500 Hours (TV engine) D Check engine cooling system.Engine Service Information Oil & Filter Change Interval Eng.
Oil ESI Oil Type Filter Filter Class Mobil CG or Delvac1 Higher 4000 hrs/ 2000hrs/ 30-00450-00 2 yrs. 3000 4000 hrs/ 30-00463-00 hrs/ 2 yrs 2 yrs. 3000 hrs/ 150-00 2 yrs. hrs/1 yr. Extended life coolant should be replaced every five years.
A more detailed description of service requirements and procedures can be found in the Service and Operations Manual for your unit. This manual may be obtained from any Carrier Transicold dealer.
Carrier Transicold Parts
RIMING YSTEM The mechanical fuel lift pump is mounted on the engine next to the injection pump. This pump has a manual plunger for priming the fuel system when the fuel tank has been run dry. To prime the fuel system, use the following steps: 1. MERGENCY ERVICE At Carrier Transicold we’re working hard to give you complete service when and where you need it. That means a worldwide network of dealers that offer 24-hour emergency service. These service centers are manned by factory trained service personnel and backed by extensive parts inventories that will assure you of prompt repair.
Fax: 1- -706- -546- -5207 P.O. Box 4805 Tel: (5255) 9126.0300 Syracuse, N.Y. 13221 U.S A Fax: (5255) 9126.0373 www.carrier.transicold.com A member of the United Technologies Corporation family.
Stock symbol UTX 2005 Carrier Corporation D Printed in U.